We at FutureWave Research are excited to guide you through the dynamic world of robotics in manufacturing. This technology is transforming industries by improving efficiency, reducing costs, and enabling new capabilities.
Understanding the synergy between robotics and artificial intelligence (AI) is the first step towards future-proofing your manufacturing process. Let’s explore how this innovative combination is revolutionizing the manufacturing landscape, driving growth, and shaping the future of production.
Robotics and AI in Manufacturing
The integration of robotics and artificial intelligence (AI) in manufacturing represents a significant leap forward in how we produce goods. It’s not just about automating tasks; it’s about creating a smarter, more efficient, and highly adaptive manufacturing environment. Robotics, essentially machines designed to carry out a series of actions automatically, becomes exponentially more powerful when combined with AI. AI brings the ability to analyze data, learn from processes, and make decisions, enhancing the capabilities of robotic systems.
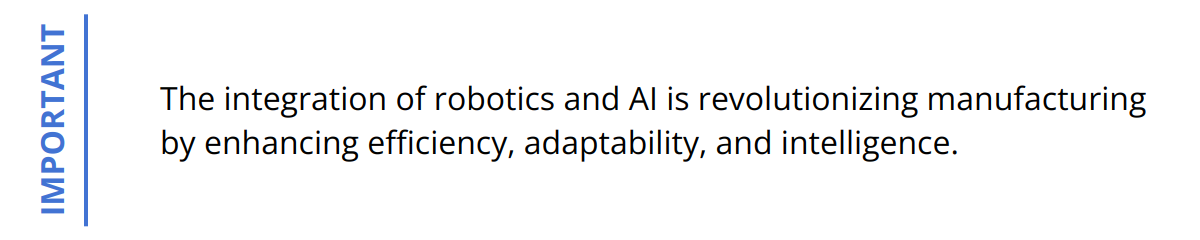
Revolutionizing Production with AI-Enhanced Robotics
AI significantly boosts the power of manufacturing robots, allowing them to handle more complex tasks, adapt to changes, and improve production outcomes. From precision assembly tasks that require extreme accuracy to predictive maintenance that forecasts machine failures before they occur, AI enables robots to perform with increased efficiency and intelligence.
The importance of robotics in modern manufacturing cannot be overstated. They offer increased productivity, reduced operational costs, and enhanced product quality. Moreover, they reduce the strain on human workers by taking over repetitive, hazardous, or physically demanding tasks. This shift not only improves safety but also allows human employees to focus on more strategic and creative tasks.
Practical Insights for Embracing Robotics in Manufacturing
- Evaluate the Production Line: Identify tasks that are repetitive, time-consuming, or hazardous. These are prime candidates for automation.
- Choose the Right Robot: Not all robotic systems are created equal. Determine whether you need a stationary robot for tasks like welding or a mobile robot for materials transportation.
- Consider AI Capabilities: AI can vastly improve the functionality of your robotic system. Look for AI technologies that can offer predictive analytics, autonomous decision-making, and real-time adaptation.
- Plan for Integration: Implementing robotic systems into your manufacturing process may require adjustments. Plan how you will integrate these systems with minimal disruption.

The Future Is AI-Driven
As we look forward, the synergy between robotics and AI in manufacturing is set to deepen. Advances in AI will unlock new levels of autonomy, efficiency, and flexibility in robotic systems. The manufacturing sector is poised to witness not just incremental improvements but transformative changes that redefine what’s possible on the production floor.
For businesses looking to stay ahead, investing in AI-enhanced robotics is not just an option; it’s a strategic necessity. The sooner companies adopt this technology, the faster they’ll reap the benefits of enhanced efficiency, cost savings, and competitiveness in the global market.
Types of Robots in Manufacturing
Exploring the variety of robotic technologies in manufacturing opens a world of possibilities. Each type of robot has its unique strengths and applications, suited for different tasks on the manufacturing floor. Here’s a closer look at articulated robots, cartesian robots, and collaborative robots (cobots), focused on how they contribute to the manufacturing process.
Articulated Robots
Articulated robots are perhaps the most recognizable, featuring rotary joints that allow for a wide range of movement. These robots are incredibly versatile, capable of performing complex tasks such as assembling, packing, and welding with precision. Their flexibility makes them ideal for operations that require reach and agility. For instance, articulated robotic arms play a pivotal role in automotive manufacturing, where they assemble parts in confined spaces that might be challenging for human workers.
Cartesian Robots
Cartesian robots, known for their linear movement, operate on three orthogonal axes (X, Y, and Z). This straightforward movement system makes them perfect for tasks that require high precision but less flexibility, like CNC machine tending, pick and place tasks, or even 3D printing. Their structured path of motion ensures consistent product quality, essential for industries where accuracy is paramount. Manufacturers should consider cartesian robots for operations that benefit from their precision and reliability.
Collaborative Robots (Cobots)
Cobots represent a significant shift in the robotics landscape. Designed to work alongside humans, cobots are equipped with safety features and sensors that allow for close human-robot interaction without the need for traditional safety barriers. This opens up a new realm of possibilities for small and medium-sized enterprises (SMEs) looking to introduce automation without extensive modifications to their existing setup. Cobots are highly adaptable and can be reprogrammed for different tasks, offering flexibility and efficiency improvements in tasks like packaging, quality inspection, or assembly.

Here are some practical tips when considering robotic solutions:
- Identify Your Needs: Evaluate the tasks that could benefit from automation. Consider the complexity, required precision, and interaction with human workers.
- Safety First: Especially with cobots, ensure the chosen technology adheres to the highest safety standards for human-robot collaboration.
- Scalability: Opt for robots that can adapt to various tasks as your business grows and needs change.
- Expert Advice: Collaborate with technology providers to select the appropriate robot type for your specific manufacturing processes.
With advancements in technology, the application of robots in manufacturing is becoming more accessible and cost-effective. Leveraging the right type of robot for specific production tasks can significantly enhance efficiency, safety, and product quality. Manufacturing leaders should stay informed about these technologies to make strategic investments that drive long-term growth.
Implementing Robotics in Manufacturing
Introducing robotics into your manufacturing process is not a decision to take lightly, but with proper planning and execution, the benefits far outweigh the initial investment and effort. Successful implementation can lead to significant efficiency improvements, cost reductions, and enhanced product quality.
Steps to Introduce Robotics into Manufacturing
The journey to implementing robotics begins with a comprehensive evaluation of your current processes. Identify bottlenecks, repetitive tasks, and areas where precision and efficiency could be improved. Following this, conducting thorough research on the various types of robotics solutions available and how they align with your specific needs is essential. It’s vital to involve your team in this process, as their insight and engagement are key to a smooth transition.
Once you’ve selected the appropriate robotic technology, planning the integration becomes crucial. Consider the layout of your manufacturing floor, the interaction between human workers and robots, and any necessary training programs to upskill your workforce. Partnering with experienced providers can offer invaluable support, from initial setup to ongoing maintenance.
Finally, monitoring performance and gathering feedback will help you fine-tune the system, ensuring optimal efficiency and productivity. Adjustments and updates may be necessary as you learn more about the capabilities and limitations of your robotics system in the context of your operations.
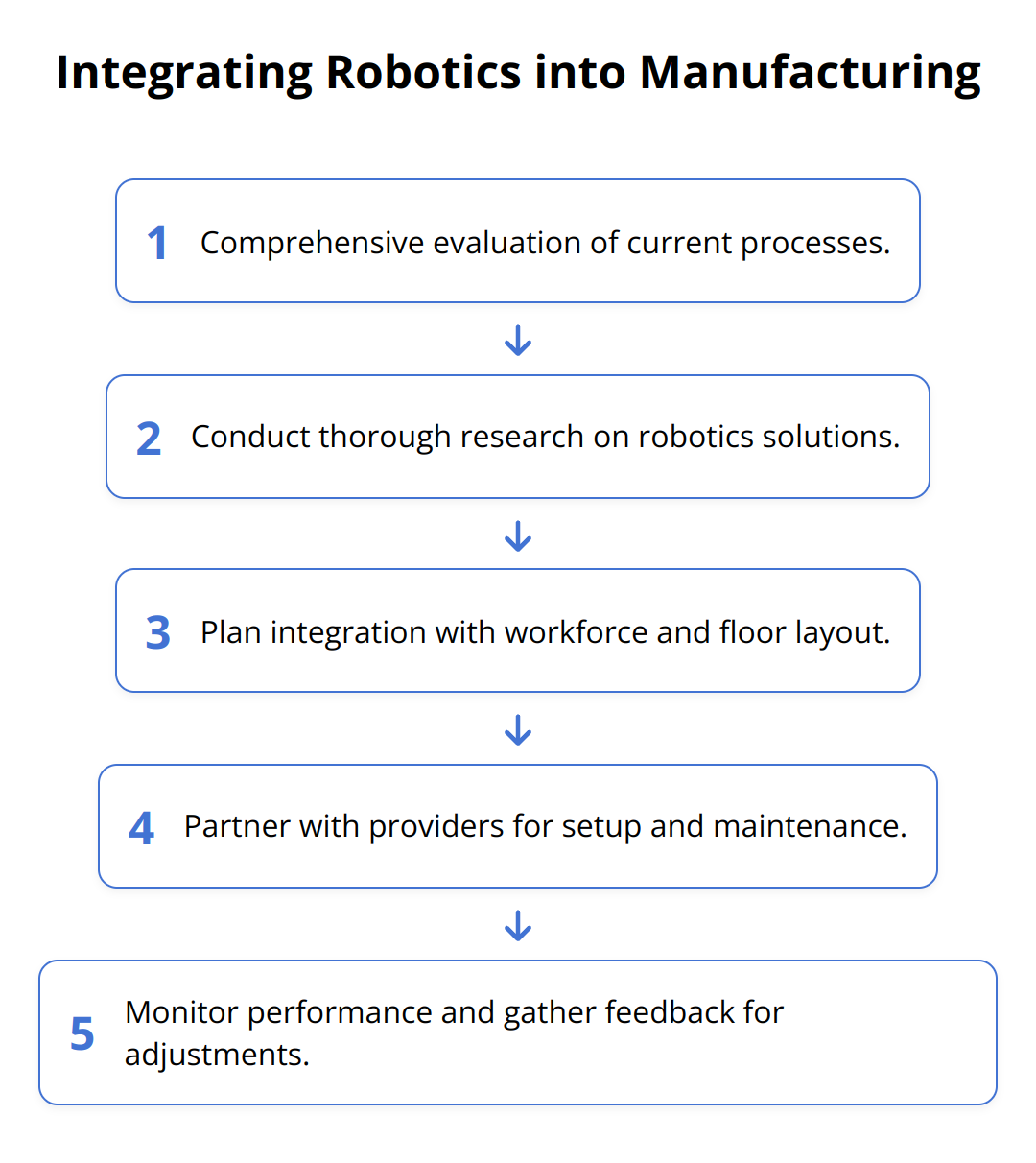
Factors to Consider When Choosing Robotic Solutions
- Compatibility with Existing Systems: Ensuring that the new robotics technology integrates seamlessly with your current manufacturing processes is key.
- Scalability: The chosen solution should be able to grow and adapt as your business and its needs evolve.
- Return on Investment (ROI): Calculate the anticipated ROI, considering factors such as productivity gains, reduced labor costs, and improved quality.
- Safety: Ensure that the robotic systems comply with all relevant safety standards to protect your team.
Success Stories: How Robotics Transformed Manufacturing Businesses
Many manufacturing businesses have seen substantial benefits from implementing robotics. For example, a leading automotive manufacturer introduced collaborative robots (cobots) into their assembly lines, resulting in a 50% reduction in production time for certain tasks. Similarly, a small electronics producer leveraged cartesian robots to automate precise component placement, increasing their product yield by 30%. These success stories highlight the transformative potential of robotics in manufacturing, underscoring the importance of embracing this technology to stay competitive.
In summary, while the journey to implementing robotics may seem daunting, the strategic benefits are clear. By carefully selecting the right technology, planning for integration, and learning from the success of others, manufacturers can achieve significant improvements in efficiency, cost savings, and product quality.
Final Thoughts
As we have explored, the integration of robotics and artificial intelligence (AI) in manufacturing is not just a trend but a transformative shift that is reshaping the industry. The power of robotics, augmented with AI’s analytical and decision-making capabilities, is creating smarter, more efficient, and highly adaptive manufacturing environments. These technologies are driving growth, improving production outcomes, and enabling businesses to stay competitive in a rapidly evolving global market.
![Key Takeaways - Robotics in Manufacturing AI [Beginner's Guide]](https://futurewaveresearch.org/wp-content/uploads/2024/03/Robotics_in_Manufacturing_AI__Beginner_s_Guide__5_2024_03_27_07_13_21_012471_00_00.png)
Looking forward, the evolution of robotics in manufacturing promises even more revolutionary changes. With advancements in AI, we can expect robotic systems to achieve new levels of autonomy, efficiency, and flexibility. This progression will not only enhance the capabilities of current systems but also open up possibilities for innovation in manufacturing processes and product development.
For manufacturers aiming to thrive in this new era, embracing robotics technology is essential. It’s about more than just automating tasks; it’s about leveraging the full potential of these technologies to optimize operations, reduce costs, and enhance product quality. The journey toward integrating robotics may seem challenging, but the strategic benefits are undeniable. By carefully selecting the right technology, planning for integration, and learning from successful implementations, businesses can achieve significant improvements and secure a competitive edge.
We at FutureWave Research are committed to guiding organizations through these dynamic technological landscapes. Our expert insights and consulting services are designed to empower clients to innovate and make informed decisions about the future of technology in manufacturing and beyond. By partnering with us, manufacturers can navigate the complexities of integrating robotics and AI into their processes, ensuring a smooth transition into a more efficient, productive, and competitive future.
In conclusion, the journey into robotics and AI in manufacturing is an exciting frontier, full of opportunities for growth and innovation. We encourage manufacturers of all sizes to explore these technologies and consider their transformative potential. With the right approach and resources, the future of manufacturing is undoubtedly bright, driven by the intelligent and strategic application of robotics and AI.